After careful consideration I have decided to transfer all hardware review activities to a new domain. I purchased Hardwareasylum.com in 2012 and have been working hard to build a new and improved Ninjalane on that domain. If you are reading this you have reached one of the archived articles, news, projects and/or reviews that were left behind during the site migration.
Please update your bookmarks and be sure to visit the new and improved Ninjalane at Hardwareasylum.com
CoolerMaster Hyper 212 Plus Heatsink Review
Author: Dennis Garcia
Published: Thursday, August 27, 2009

Benchmarks
The CoolerMaster Hyper 212 Plus is designed for Intel Socket LGA1366 / 1156 / 775 and AMD Socket AM3 / AM2 / AM2+ processors. Here is an overview of the system and testing methodology.
The system as it was tested
EVGA X58 LE Intel X58 Chipset
Core i7 920 (2.66Ghz) 4 x 256KB L2, 8MB L3 Cache 4.8GT/s QPI
CoolerMaster Hyper 212 Plus
OEM Heatsink
Smart Guardian was used to obtain and record system temperature data and being that this is a quad core processor we need something that will work across all of the cores at once. For this task we're using a new version of Prime95 (p95v255a) that will allow you to spawn (n) instances to test with.
In our case we choose 8.
Core i7 920 (2.66Ghz) 4 x 256KB L2, 8MB L3 Cache 4.8GT/s QPI
CoolerMaster Hyper 212 Plus
OEM Heatsink
Smart Guardian was used to obtain and record system temperature data and being that this is a quad core processor we need something that will work across all of the cores at once. For this task we're using a new version of Prime95 (p95v255a) that will allow you to spawn (n) instances to test with.
In our case we choose 8.
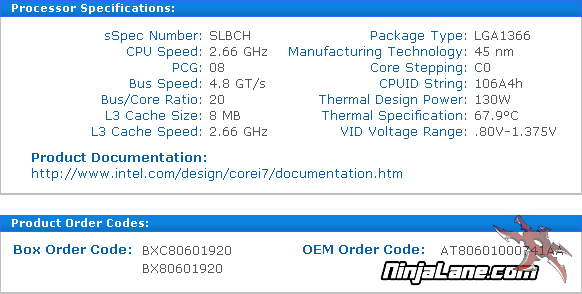
Editors note: Even though the Windows Vista task manager reported 100% processor usage we could never attain a 100% of the rated heat output as documented by Intel (see below) when using Prime95 as a basis for that heat production. Knowing this we ran the stress test until the maximum temperature was attainted and stabilized.
Other things to consider when judging software induced heat output.
a) Clock throttling by the processor at high temperatures.
b) Normal software isn't designed to produce maximum heat output.
c) Variances of cooling temperature.
d) Variances in CPU load.
e) Inaccuracies in thermal diode readouts.
Of course the list goes on..
Our testing methodology is aimed to provide a real world look into this heatsink given the test system provided.
Other things to consider when judging software induced heat output.
a) Clock throttling by the processor at high temperatures.
b) Normal software isn't designed to produce maximum heat output.
c) Variances of cooling temperature.
d) Variances in CPU load.
e) Inaccuracies in thermal diode readouts.
Of course the list goes on..
Our testing methodology is aimed to provide a real world look into this heatsink given the test system provided.
Default Speed
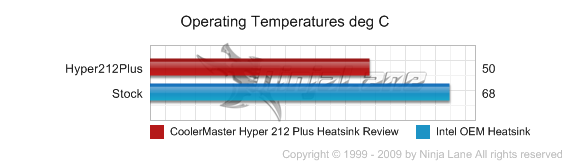
A C/W rating can quickly be calculated using this formula.
C/W = (CPU temp - Ambient temp)/(Variance(%) * CPU Watts)
Allowed variance for this test = 85%
CPU Watts = 130W
0.20 C/W = (50C - 27.5C)/(.85(130W))
C/W = (CPU temp - Ambient temp)/(Variance(%) * CPU Watts)
Allowed variance for this test = 85%
CPU Watts = 130W
0.20 C/W = (50C - 27.5C)/(.85(130W))
Overclocked
For this next test the FSB was cranked up to 200Mhz and the test was re-run. 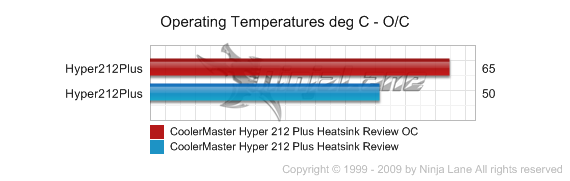
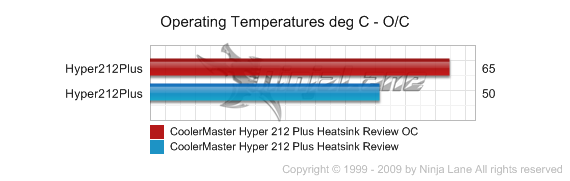
To calculate a new C/W rating for this test we will need to factor in the increased processor wattage. The formula and constants for this are listed below.
ocC/W = dCPU Watts * (ocMhz / dMhz) * (ocVcore / dVcore)2
ocMhz = 4000
dMhz = 2660
ocVcore = 1.30
dVcore = 1.20
The variance still applies for our C/W calculation
Allowed variance for this test = 85%
CPU Watts = 229W
0.19 C/W = (65C - 27.5C)/(.85(229W))
ocC/W = dCPU Watts * (ocMhz / dMhz) * (ocVcore / dVcore)2
ocMhz = 4000
dMhz = 2660
ocVcore = 1.30
dVcore = 1.20
The variance still applies for our C/W calculation
Allowed variance for this test = 85%
CPU Watts = 229W
0.19 C/W = (65C - 27.5C)/(.85(229W))
Benchmark Conclusion
In our heatsink and waterblock tests we don't really focus on overall load temperatures but rather how well the product can remove heat given a specified heat load. Since this is a real world testing method we need to take into consideration real world variables and estimate tolerances. This is why we normally only apply 85% of the total wattage output to our heat calculations.
The resulting C/W number is used to rate how efficient a heatsink or waterblock is based on the given heat load. These numbers can be used to determine heat capacity, the larger the difference the less efficient the heatsink is. (aka not good for overclocking)
Here we have a heatsink that can clearly handle more than our system can dish out. All too often we find a rather pronounced variance between the default and overclocked speeds which is sometimes good and sometimes bad. For these tests you'll see that the resulting C/W numbers have actually reversed meaning that we have not even gotten close to the thermal limit of this cooler.
Keep in mind these calculations are provided for demonstration purposes only and may not reflect the actual lab tested C/W rating, but we're pretty close.
The resulting C/W number is used to rate how efficient a heatsink or waterblock is based on the given heat load. These numbers can be used to determine heat capacity, the larger the difference the less efficient the heatsink is. (aka not good for overclocking)
Here we have a heatsink that can clearly handle more than our system can dish out. All too often we find a rather pronounced variance between the default and overclocked speeds which is sometimes good and sometimes bad. For these tests you'll see that the resulting C/W numbers have actually reversed meaning that we have not even gotten close to the thermal limit of this cooler.
Keep in mind these calculations are provided for demonstration purposes only and may not reflect the actual lab tested C/W rating, but we're pretty close.
